Performance of a stone crusher plant depends on the configuration of the production units. The use of impact and rolling compression makes the stone crusher plant produce a higher output with low power and noise level. A jaw crusher is a common machine in a stone crushing plant and can work on a variety of stones. The gap setting of this type of crusher determines its output size. A tighter gap setting results in smaller output and a lower throughput capacity.
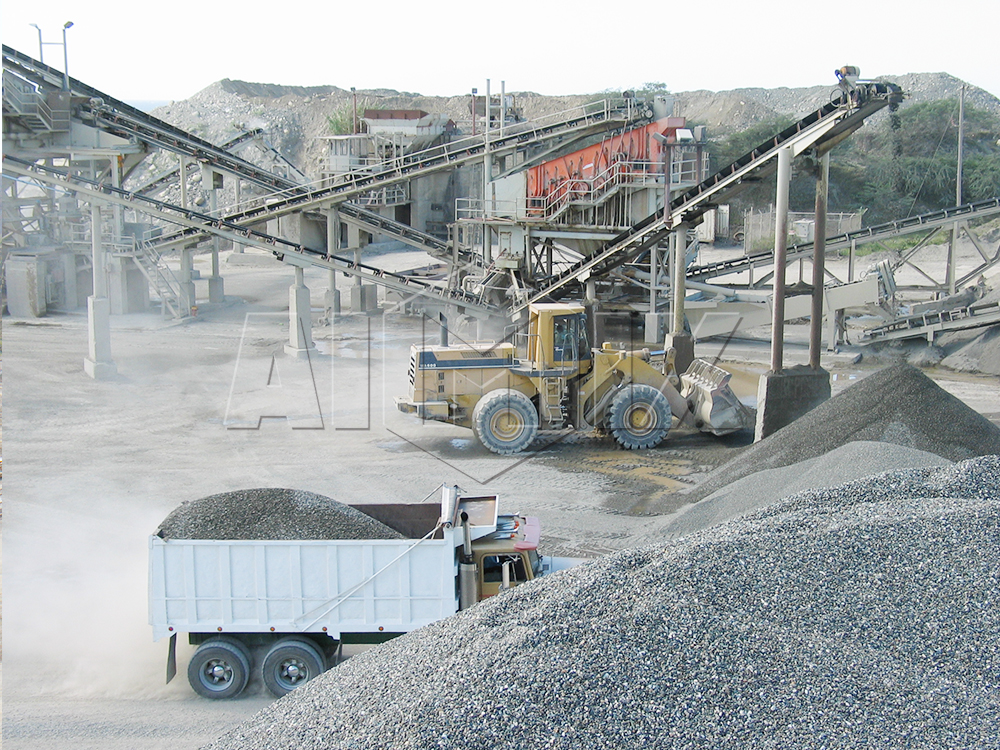
Configuration of production units affects performance
The configuration of production units in a stone crusher plant(planta trituradora) affects the overall plant performance. This is the result of an optimization process that involves the use of computerized reasoning to simulate the operation of a real plant. The model is used to shape agent degree information for the crushers and improve the final product gradation. Its use is discussed in this article and strategies to optimize the model are sketched.
Impact and rolling compression make the stone crusher plant yield a higher output with a lower noise level and power consumption
The impact and rolling compression crushers work in tandem to produce the highest possible output with minimum noise and power consumption. Both impact and rolling compression produce equal amounts of pressure, resulting in a lower power consumption and noise level. The crushers are made to withstand a variety of abrasive surfaces and are particularly efficient in the crushing of hard rocks.
Symons cone crusher
A Symons cone crusher is a proven choice for high-performance crushing. Its advanced hydraulic system allows it to operate efficiently and reliably, allowing you to focus on other matters that need attention. The cone crusher should be choke-fed for maximum efficiency and productivity, and it must be properly sized for optimal yield. It must also be fed with an appropriate circuitry, including a hopper and feeder. A properly-sized feed system reduces side loading and premature wear.
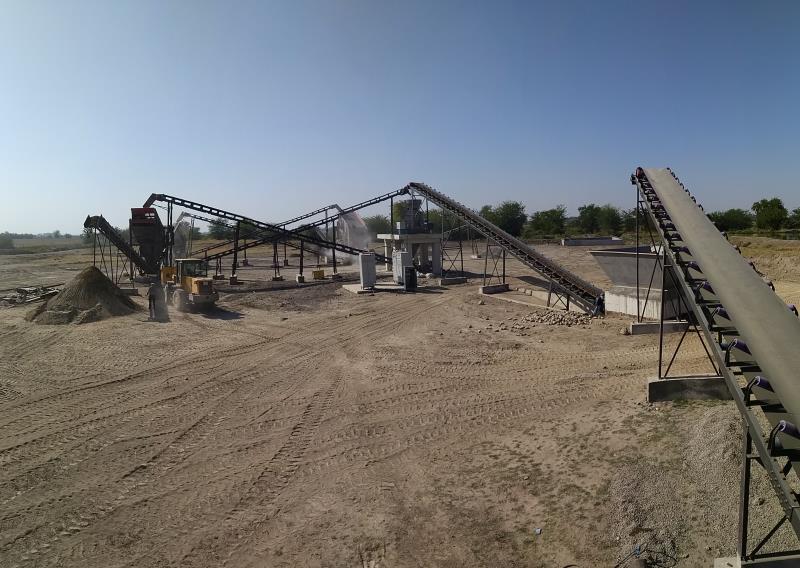
Gyratory crusher’s cavity profile
This paper presents a numerical model of the Performance of a Gyratory crusher plant, which was developed to simulate the behavior of a crushing plant(plantas de concreto en venta). It uses a combination of a numerical and physical approach to solve the problem. Its results show the impact of operational parameters on the performance of a gyratory crusher. A comparison is made between the base case and the non-uniform filling case. The results of simulations of varying open-side settings, rpm, and Bond’s equation are also presented.
Adequate screening capacity downstream of the crushing circuit
While most producers would want to increase the tons per hour of material that can pass across the screen, there are many ways to increase screening capacity without sacrificing efficiency. Screens are used to separate aggregate material into different sizes. Depending on the size of the stone, the screens may have one or more decks. Screening efficiency is improved by setting the screen’s parameters. A vibrating screen will work at its maximum capacity when it is properly adjusted.
Gyratory crusher’s feed gradation
A Gyratory crusher reduces the size of rocks to a minimum size of about 10 to 15 cm by compressing them. This process reduces the size of rock particles by as much as five to eight times. The size of feed particles is controlled by gyratory’s setting. This type of crusher is typically equipped with hydraulic setting adjustment systems to control the feed gradation and product size. In primary crushers, the gyratory is set to a minimum of 190 rpm. A secondary cone crusher operates at a minimum of 0.75 gyratory setting. Discover here: https://aimixgrupo.com/planta-de-concreto-premezclado-en-venta/
Gyratory crusher’s operating principle
The Gyratory crusher’s operating principle in a stone crusher plant is very similar to that of a jaw or cone-type crusher. In a Gyratory crusher, the crushing head is large, and the area of the discharge opening is directly proportional to the head diameter. The crushing chamber is deep and curved, providing a deep and acute crushing angle while maximizing capacity. The contour at the bottom of the crushing chamber allows for various initial settings. Lower tier concaves are installed to achieve the desired setting and capacity.
AIMIX stone crusher plant
The AIMIX stone crusher plant’s performance is highly dependent on its configuration. Depending on the size of the quarry, rock feed materials, and usage of the final products, different plants can have vastly different layouts. The process of design is usually based on connecting the production unit models. The input and output characteristics are analyzed in detail. The layout of a crushing plant must include the sequence of product demand, the desired product quality and price, and operating costs.